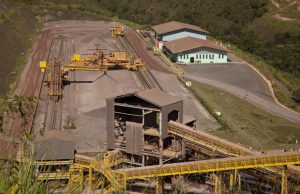
Por Tébis Oliveira
Em 2008, quando iniciou sua operação, a unidade de Miraí (MG), da Companhia Brasileira de Alumínio (CBA), já tinha sua usina de beneficiamento totalmente automatizada. O projeto foi concebido para evitar os problemas verificados em outra planta da companhia, em Itamarati de Minas, no mesmo estado. “Lá, os controles da vazão de água na alimentação da planta e amostragem, por exemplo, eram manuais, dependiam de mais operadores e não geravam resultados em tempo hábil. As manutenções preditivas não tinham acompanhamento on line, nem registro dos parâmetros de desempenho dos equipamentos para detecção antecipada de falhas”, explica o gerente de Miraí, Christian Fonseca de Andrade.
O resultado foi uma planta de beneficiamento com maior controle operacional, enxuta, segura e de máxima utilização, diz o gerente. Além da usina, são automatizados, desde 2008, o sistema de pesagem rodoviária da mina e, desde 2016, a amostragem de minério ROM e beneficiado. Agora, está em estudo um projeto para o sistema de despacho, visando o monitoramento de todos os equipamentos, incluindo dados como localização nas frentes de trabalho, paradas de manutenção, tempo de operação e produtividade, entre outros.
O caso de Miraí não é isolado. Na Copebras, da CMOC (Chyna Molibdenum Corporation), a Mina Chapadão, em Ouvidor (GO), possui 70% dos processos automatizados e terá 100% até 2019, englobando as áreas de britagem, empilhamento e concentração. O mesmo ocorre na Niobras, produtora de nióbio do mesmo grupo, que parte este ano para a automação do sistema de despacho. Na Votorantim Metais, em Minas Gerais, a mina subterrânea de Morro Agudo deve implantar no semestre próximo o desmonte remoto, enquanto na mina de Vazante, que teve a moagem e flotação automatizadas em 2006, está em fase de validação de um projeto de gestão de ativos e monitoramento de processos.
Controle Integrado
Através de um sistema supervisório instalado em uma sala de controle de Miraí, operadores verificam e alteram parâmetros dos equipamentos como velocidade de rotação, temperatura de acoplamentos, frequência e corrente elétrica, entre outros. O controle se estende aos indicadores físicos de processo: taxas de alimentação e produtividade e de vazão e consumo de água, tanto a recirculada através da barragem de rejeitos (99% do consumo), quanto a captada, para cumprimento dos limites de outorga. São automáticos, ainda, o intertravamento em questões de segurança e o acionamento e desligamento da planta.
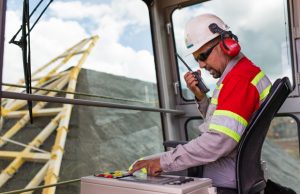
Também o sistema de pesagem rodoviária dos caminhões que transportam ROM e minério beneficiado, implantado em 2008 e modernizado em 2016, é automatizado em Miraí, registrando a Tara (peso líquido carregado), hora da pesagem, origem ou destino e placa dos veículos, entre outros dados. As informações são coletadas por painéis eletrônicos e antenas transponder instalados nas três balanças e transmitidos por rádio frequência à sala de controle. O mesmo sistema de pesagem foi instalado nas unidades de Poços de Caldas e Itamarati de Minas, da CBA.
Em 2016, a companhia adotou duas outras inovações. Uma delas, no sistema supervisório, foi a integração de dois amostradores automáticos, que substituíram a coleta manual de amostras de minérios ROM e beneficiado, otimizando a segurança operacional e os níveis de utilização da planta, além de reduzir custos e aumentar a capacidade de produção. Outra foi a construção de uma estação de tratamento de água (ETA), com capacidade de mil m³/h, com um sistema autônomo para controle do tratamento da água retirada da barragem.
Para automatizar a usina, a ETA e o sistema de pesagem rodoviária de Miraí, a CBA investiu R$ 7,1 milhões. À época, foi difícil convencer os envolvidos dos resultados verdadeiros e mensuráveis do projeto, diz Andrade, Com o tempo, os fatos falaram por si: a produtividade da usina passou de 250 t/h, em 2008, para 356 t/h, em 2012, e alcançou 436 t/h, em 2016, um aumento de quase 75%.
Automação da Unidade Miraí – CBA | |
Instalação | Tecnologia |
Usina de Beneficiamento | Técnicas de controle proporcional integral derivativo (PID), protocolo de rede PROFIBUS |
Tecnologia ABB c/utilização do sistema supervisório 800XA | |
Estação de Tratamento de Água | Tecnologia Rockwell c/utilização do sistema supervisório Factory |
Sistema de Pesagem Rodoviária | Tecnologia CA (Controle de Acessórios Unificados) da Saturno p/a balança |
Tecnologia JAD – Junção Analógica Digital (substituiu o sistema de pesagem de células de cargas digitais na balança) |
Operação Remota
Na Copebras, da CMOC (Chyna Molybdenum Corporation), cerca de 70% dos processos da Mina Chapadão, localizada em Ouvidor (GO), são automatizados. Na britagem é usado o sistema supervisório SDCD (Sistema Digital de Controle Distribuído), da japonesa Yokogawa, que controla e monitora os dados dos equipamentos e permite sua operação remota. A partir do SDCD, é possível acompanhar a temperatura dos equipamentos e a taxa de alimentação de rocha fosfática que chega nas usinas, após a britagem e homogeneização do minério, diz o coordenador de manutenção da empresa, Rogério Stoppa. O mesmo sistema será implantado, até 2019, na Usina 76, concluindo a automação de todo o complexo da Mina Chapadão. Neste ano, a Copebras está investindo na automação dos processos de medição de densidade e vazão e de alimentação da moagem secundária.
Airton Alves Rodrigues Junior, engenheiro eletricista da mineradora, diz que a automação teve como objetivos o controle 24 horas da cadeia operacional de britagem, empilhamento e concentração e a formação de um histórico operacional das unidades. “Outro ganho é a tomada rápida de decisões a partir da identificação dos problemas”, acrescenta.
Na Niobras, área de negócios de nióbio da CMOC, os processos de britagem, homogeneização e beneficiamento da mina Boa Vista, onde ficam as plantas de concentração de rocha fresca (BVFR) e de minério oxidado (BV), assim como na Planta Tailings, de recuperação de rejeitos, também são automatizados e operados remotamente. Um exemplo é a empilhadeira-retomadora FAM da BVFR, que segue uma programação diária, de acordo com o planejamento da produção, a partir de um sistema Schneider integrado ao projeto da unidade, inaugurada em 2014. Na BV, um sistema da GE foi implantado após o início das operações, enquanto o da Planta Tailings, da Yokogawa, começou a operar em 2008, sendo atualizado nos anos posteriores.
Antes da automação, lembra João Paulo de Castilho, coordenador de engenharia de manutenção da Niobras, ocorriam paradas não programadas, não havia padronização das atividades e a variabilidade dos processos era maior, dificultando o controle da produção. Neste ano, a empresa está atualizando a linha de britagem da liga de ferronióbio, substituindo o sistema supervisório e migrando seu banco de dados para um servidor de automação central, e deve automatizar também seu sistema de despacho. Os investimentos em automação na Niobras e Copebras totalizaram cerca de R$ 11 milhões, enquanto na BVFR foram aplicados US$ 380 milhões.
Plano Diretor
Com implantação prevista para o segundo semestre deste ano, a mina subterrânea de Morro Agudo, em Paracatu (MG), da Votorantim Metais (VM), terá uma nova tecnologia de desmonte projetada pela australiana Orica, que permitirá sua execução a partir da superfície. Um teste do processo, inédito na América Latina, foi realizado em outubro de 2016, comprovando a redução de atrasos durante as trocas de turno e descida dos funcionários na mina.
Segundo o gerente geral da unidade, Victor Silva, a mina possui quatro turnos de seis horas e, no método atualmente empregado, é necessário evacuar todos os funcionários ao final de cada turno, para a liberação do desmonte com explosivos. Como a mina possui 120 km de galerias, o tempo consumido para a retirada das equipes e o deslocamento da equipe de blaster é muito longo. Além do ganho de tempo, que será aproveitado em outras atividades como manutenção de equipamentos e preparação de novas frentes de lavra, a nova técnica elevará os níveis de segurança operacional.
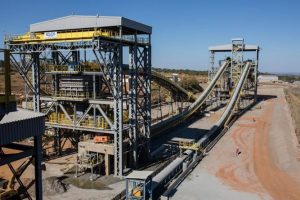
Para o acionamento remoto dos explosivos, todas as frentes de lavra e desenvolvimento terão sua infraestrutura de cabeamento atualizada. O projeto teve investimentos de cerca de R$ 1 milhão e pode, futuramente, ser entendido às minas de Vazante (MG) e Cerro Lindo (Peru), também subterrâneas, e para a mina de Ambrósia (MG), em fase de pré-stripping.
Na mina de Vazante, aliás, desde 2006 está instalado um sistema APC da Metso nas áreas de moagem e flotação, com ótimos resultados operacionais e de recuperação de minério, garante Marco Carrete, gerente de automação da VM. Em 2015, foi iniciado um projeto piloto de gestão de ativos e monitoramento de processos das mesmas áreas via IIoT, desenvolvido pela GE e em fase de validação de resultados.
Segundo Carrete, a automação das operações é um conceito que integra a cultura empresarial da companhia, que estimula a busca por soluções que possam aumentar a eficiência dos processos, diminuindo a variação da produção e, com isso, reduzindo o consumo de alguns reagentes de alto custo. Atualmente, está sendo elaborado um Plano Diretor de Automação, que deve abranger todas as unidades da empresa e visa a melhoria de sua performance, estabilidade operacional, redução de custos e aumento de competitividade no cenário mundial.
Leia também: