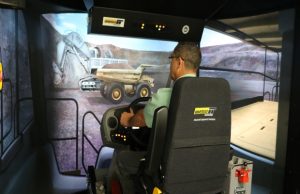
Há mais de dez anos, a Vale emprega simuladores virtuais no treinamento de seus operadores. Até 2014, eram quatro equipamentos. Em 2015, foram adquiridos outros sete. Atualmente, quatro ficam no Sistema Norte (Pará) e sete no Sistema Sul (Minas Gerais). Oito são usados para caminhões off road, dois para escavadeiras e um para tratores de esteira. Os modelos são da Immersive Technologies, CAE Terra Mining Simulator e 5DT (Fifth Dimension).
A decisão de adotar o treinamento virtual, explica Kesley Julianelli, gerente de Competitividade e Produtividade de Minério de Ferro da Vale, visou a maior capacitação dos operadores para a obtenção de índices melhores de segurança, produtividade e custo operacional. “Reduzimos o número de acidentes e ampliamos o controle em situações de emergência. Antes, os funcionários só conseguiam aplicar a teoria aprendida em situações reais”, justifica.
A condução mais eficiente pelos operadores também traz ganhos de produtividade e disponibilidade dos equipamentos, aumenta o fator de enchimento de carga e a carga média transportada e reduz os tempos de manobra e, no caso das escavadeiras, os tempos de giro. Entre os custos operacionais, destacam-se a redução do consumo de combustível e de gastos com manutenção e o aumento da vida útil dos pneus e componentes das máquinas. O uso de simuladores também eliminou o emprego de equipamentos reais para os treinamentos, evitando danos por imperícia e mantendo sua taxa de utilização em campo.
Aproveitamento
Para os operadores novatos, diz Julianelli, a simulação é uma oportunidade de primeiro contato com os equipamentos em um ambiente seguro onde as condições de operação são reproduzidas em realidade virtual com alta fidelidade. “Além do aumento da capacitação técnica, percebemos uma maior satisfação pessoal dos treinandos, com impacto positivo no clima organizacional da empresa”, acrescenta o gerente. Para os empregados já experientes, o curso é focado na identificação dos principais vícios ou falhas operacionais, que são corrigidos pelo instrutor.
Cada sessão ou cenário de treinamento possui 40 minutos de duração, totalizando 4 h de capacitação, em média. O treinamento teórico é o mesmo para todos os operadores, mas a capacidade de aplicá-lo em campo varia de um para outro. “Cada operador leva o tempo que for necessário para o seu desenvolvimento, tornando o treinamento mais individualizado em função de seu ritmo pessoal”, explica o gerente. A sistemática permite, ainda, medir o percentual de melhora em cada KPI (indicador operacional) verificado. Mais de 10 mil operadores da Vale já passaram pelos simuladores até hoje.
Em termos técnicos, Julianelli lembra que os simuladores mais antigos apresentavam falhas nos compressores que acionavam os cilindros da base de movimento. Nos mais novos, há alguns problemas no sistema de refrigeração e na manutenção dos projetores. Também há situações que, apesar de reais, ainda não podem ser simuladas. Uma delas é a superfície irregular na área de movimentação do caminhão off road, que pode ocasionar seu tombamento.
Aprendizado
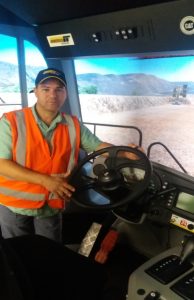
Ronaldo Cristino opera equipamentos na mina Capão Xavier, no Sistema Sul da Vale, em Nova Lima (MG), desde abril de 2013. Mas foi antes, quando começou a operar uma escavadeira na Mina de Tamanduá, na mesma cidade, que ele fez seu primeiro treinamento em um simulador. Faria um segundo, depois, para operar o caminhão 775 Caterpillar.
Entre um curso e outro há diferenças, diz Cristino. “No primeiro, tudo o que aprendi sobre o equipamento foi no simulador. No segundo, eu já tinha habilitação na categoria “D” e experiência na área”, lembra. Para ele, o simulador muda toda a operação para quem já dirige equipamentos porque identifica os erros cometidos no dia a dia. O treinamento também lhe deu dicas de economia e segurança. ”Aprendi que podemos cuidar melhor do equipamento e economizar combustível com algumas atitudes. O bom disso é que não contribui somente para a vida profissional dos operadores, mas também para o meio ambiente”, explica.
Faça o download da matéria na íntegra e compartilhe.