Praticamente todas as mineradoras possuem algum sistema de correia transportadora para escoar o fluxo interno de seus produtos entre a mina e a usina, nas interligações da usina de beneficiamento, entre a usina e o pátio de materiais e entre o pátio e a expedição. Nem sempre os projetos permitem que o sistema se apoie apenas em cavaletes fixados no solo, exigindo galerias de sustentação aérea, que vencem altura e vãos.
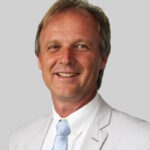
Trata-se de um sistema operado com taxa de utilização muito alta, visto que todo o fluxo de material é circulado em algum momento por cada transportador. A interrupção da operação de algum transportador praticamente paralisa em parte ou todo o fluxo produtivo da mina. “Assim, a discussão de paradas para manutenção preventiva, corretiva ou mesmo para a necessidade de repontenciar a capacidade produtiva do sistema é assunto frequente entre as equipes de planejamento, operação, manutenção e investimento das operações minerais. Afinal de contas, todo o caixa da empresa passa pelas correias transportadoras”, afirma Alexander Biskupski, diretor operacional da Bolbi.
Escoramento – A empresa atendeu à demanda de uma grande mineradora no Norte do país que, durante uma inspeção de campo, detectou a ocorrência de corrosão em uma séria de componentes da estrutura metálica de suporte de um transportador de correia, com perda de material nas colunas de sustentação, longarinas e montantes diagonais das treliças da galeria. O problema, num equipamento que fazia a interligação de fluxos na usina de beneficiamento da mina, não só aumentava o risco de acidentes envolvendo funcionários próximos, como poderia paralisar toda a planta. A decisão imediata da empresa foi reduzir a taxa de carregamento para minimizar o risco de colapso da estrutura.
Acionada pela equipe de engenharia da mineradora para avaliação e elaboração de uma solução urgente, a Bolbi propôs o escoramento estrutural do transportador. A medida, explica Biskupski, permitiu que a montagem dos equipamentos necessários à correção do problema fosse realizada com o transportador em funcionamento, sem interrupção da alimentação elétrica e da automação de interligação da usina, que passava pelo bandejamento do transportador, bem como do sistema de combate a incêndio.
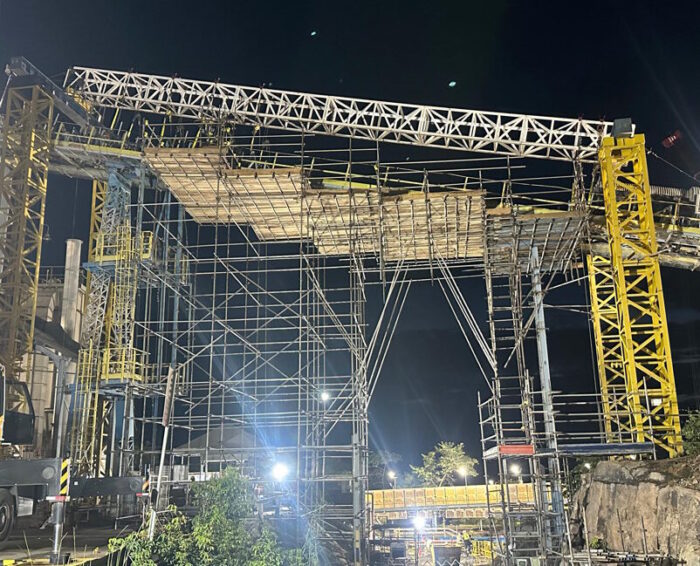
Todo o trabalho de campo foi antecipadamente simulado por uma equipe de engenheiros da Bolbi, através de programas e cálculos específicos, garantindo o respaldo técnico da atividade. O objetivo da Bolbi era, além de trabalhar com uma metodologia tecnicamente confiável, prever todas as possibilidades de riscos de acidentes, desde a fase de montagem dos equipamentos até sua operação e desmontagem. “Com um trabalho de inteligência incorporado ao projeto, conseguimos cumprir todas as normativas de segurança impostas pela legislação e as boas práticas aplicadas a clientes”, conta Biskupski.
Quando o fluxo de produção foi paralisado, as equipes de manutenção da mineradora, trabalhando em diversas frentes de trabalho simultaneamente, substituíram duas colunas de sustentação e diversos componentes da galeria. As partes remanescentes do transportador foram suportadas pela estrutura montada pela Bolbi, resistindo inclusive às variações bruscas de temperatura e fortes rajadas de vento que ocorriam na região.
A intervenção da Bolbi, diz o diretor operacional, com mobilização rápida de sua equipe, asseguraram a redução do tempo de paralisação da usina, a permanência da conexão dos sistemas elétrico, de automação e incêndio, a agilidade na montagem dos equipamentos para realização do escoramento estrutural e as condições de segurança em campo.
Foto em destaque: Guindaste empregado na montagem de suporte (Bolbi/Divulgação)