Em agosto de 2015, a Kinross iniciava a implementação do sistema MineStar na mina Morro do Ouro, em Paracatu (MG). Ferramenta de gestão integrada, a tecnologia permite o monitoramento e otimização do desempenho das frotas de perfuração, carregamento, transporte e infraestrutura da mineradora.
Os controles, em tempo real, se estendem a indicadores de ciclo e eficiência dos equipamentos, como a utilização física e disponibilidade, apontamentos de manutenção, atrasos operacionais, telemetria, qualidade do material e precisão dos projetos. “A análise desses dados permite estudos robustos e sustenta ações de melhoria no processo de produção além de suportar decisões operacionais e estratégicas de curto e longo prazo da empresa”, explica Marília Santos, engenheira plena de Mina da Kinross.
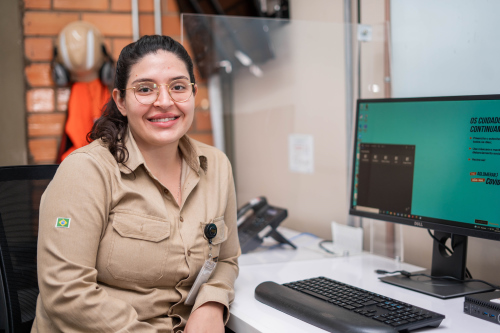
O MineStar foi configurado para operar no modo Fleet, sendo embarcado em 35 caminhões 793D Caterpillar, e no modo Terrain, atendendo a quatro escavadeiras – três elétricas e uma mecânica -, três carregadeiras 994F Caterpillar e a 10 tratores de esteiras.
Em 2020, a Kinross adotou outra plataforma digital – o Work Order -, sistematizando as ordens de serviço de suas áreas de manutenção (Saiba mais na parte final deste texto).
Gestão e benefícios
A operacionalização do MineStar depende de uma rede Wireless robusta, confiável e com capacidade de suportar a transmissão de dados do sistema, aliada aos hardwares embarcados nos equipamentos. Sua gestão é feita por meio de três servidores: um servidor de aplicação, que gerencia os projetos, as classes de equipamentos e os controladores de despacho; um servidor de banco de dados SQL Server e um terceiro para relatórios, todos hospedados em um cluster de servidores em ambiente VMware. Por meio da plataforma BOE/BI SAP Business Objects são consolidados os relatórios de KPIs de otimização do sistema. A consolidação de produtividade ocorre hora a hora, permitindo a imediata tomada de decisões.
O sistema dispara alertas, em tempo real no caso de inconformidades, como equipamento fora de curso no trajeto; abuso de mudança de marcha; excesso de velocidade e de carga; controle de massa disponível no modelo de blocos; e nível de combustível. Ao receber o alerta, o controlador de despacho orienta o operador sobre a melhor ação a ser tomada, até mesmo a de parada para manutenção, se for o caso.
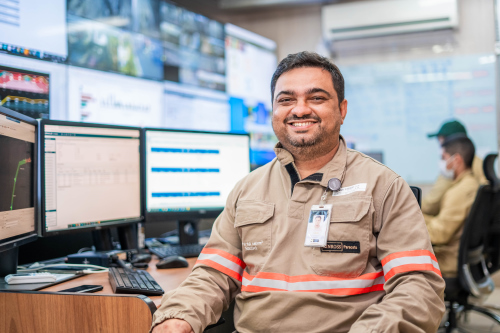
Passados seis anos da adoção da ferramenta, os principais ganhos registrados, segundo Junio Sobrinho, supervisor de Tecnologia de Mina da Kinross, foram: o monitoramento da situação e condições dos equipamentos em tempo real; ganhos de qualidade e confiabilidade das informações para as áreas de planejamento de lavra; ganhos na performance topográfica da área de operação e melhoria dos KPIs operacionais. Também foram verificados o aumento na aderência das atividades executadas aos parâmetros planejados e da eficiência operacional, segurança e produtividade, com redução dos custos operacionais.
Um exemplo de aumento de eficiência é o dos caminhões 793D – cerca de 10%. Além disso, a combinação do sistema de telemetria à expertise da engenharia de manutenção da mina, diz Marília, fez com que essa frota alcançasse uma disponibilidade física superior a 80%. A automação também otimizou o nivelamento das praças de desmonte de rocha.
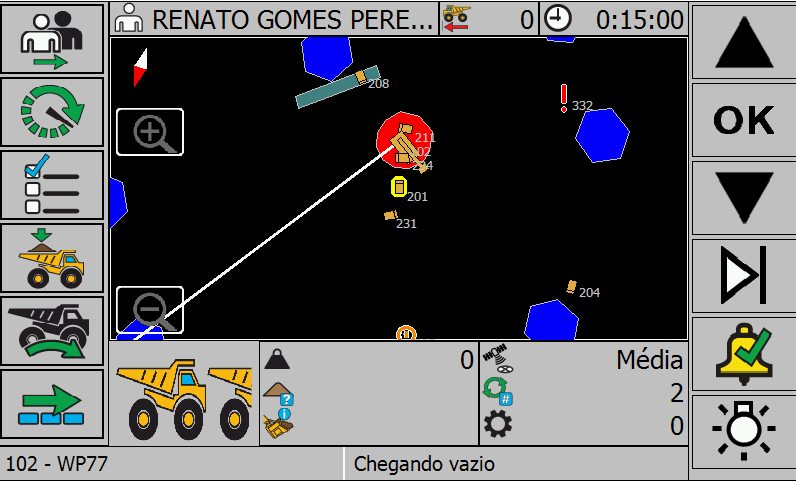
Foto ano destaque: Operação de escavadeira elétrica monitorada pelo Sistema Terrain
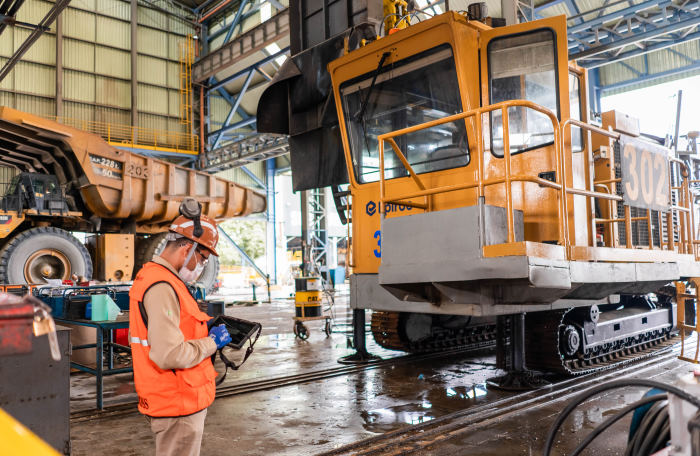
Digitalização de ordens de serviço otimiza manutenção
Outra plataforma digital – a Work Order (WO) – foi implantada pela Kinross em 2020. A solução visa mobilizar e digitalizar os processos das ordens de serviço de manutenção, eliminando papeis e reduzindo o retrabalho e os atrasos no lançamento das informações no sistema. A ferramenta utiliza um servidor de aplicação e uma base de dados, integrados ao sistema de manutenção, tablets e uma rede wi-fi, explica Lucas Piau, chefe de Tecnologia da Informação da Kinross.

Por dia, são emitidas entre 4 e 5 mil OS para manutenções preventivas e corretivas. Antes do WO, elas eram geradas em papel pelos programadores, impressas, separadas e distribuídas para as equipes. “Uma vez preenchidas pela equipe de campo, eram escaneadas e tinham seus dados digitados e inseridos no sistema pelos programadores. Com a digitalização do processo, o empregado recebe a ordem via tablet, preenche, fotografa e envia as informações diretamente no sistema”, conta Felipe Sousa, chefe de Planejamento de Manutenção da Kinross.
Para Piau, a dinâmica anterior era mais susceptível a falhas, como a de visualização imperfeita dos documentos, e delays no registro causados pelo tempo consumido no lançamento das informações. Outros ganhos incluem a redução de documentos impressos; do tempo para baixa semanal das WO pelos programadores e de follow up de conclusão das tarefas (apontamento hora a hora com reports diários aos supervisores), além da maior aderência dos apontamentos h/h nas OS.

Hoje, todas as OS já nascem como uma WO criada no status 01, trabalhada pelo planejamento até o status 45, liberada para execução no status 55 e encerrada no status 80, diz Sousa. As programações são definidas em reuniões semanais, quando se discute as demandas e é estabelecido o plano de execução da semana seguinte.
Após programadas, as OS são geradas e liberadas para execução na sexta-feira da semana anterior à programada. A execução pode entregar as ordens diariamente ou, no máximo, até a terça-feira da semana seguinte ao seu atendimento. Todas trazem dados de apontamento de horas e observações feitas em campo pela execução. Essas informações são tratadas pelo programador e inseridas no sistema no momento da baixa.
Atualmente, a gerência de Manutenção da Kinross conta com as áreas de Oficina de Equipamentos Móveis (214 empregados) e de Manutenção Industrial (278 pessoas), ambas compostas pelos departamentos de Planejamento e de Execução.