A Mineração Caraíba (MCSA), produtora de cobre sediada em Jaguarari, no norte da Bahia, adotou em abril de 2021 o sistema Mining Control como software de controle operacional e de gerenciamento de equipamentos. A solução foi uma resposta à complexidade envolvida na gestão de dados de produção, operação, desempenho da frota de equipamentos e controle de manutenções da empresa. Os estudos e testes foram iniciados em 2020, visando o desenvolvimento de um sistema exclusivo à mineração subterrânea, para melhorar a gestão de indicadores operacionais (UF e PDT) e de manutenção dos equipamentos (DF, MTBF e MTTR).
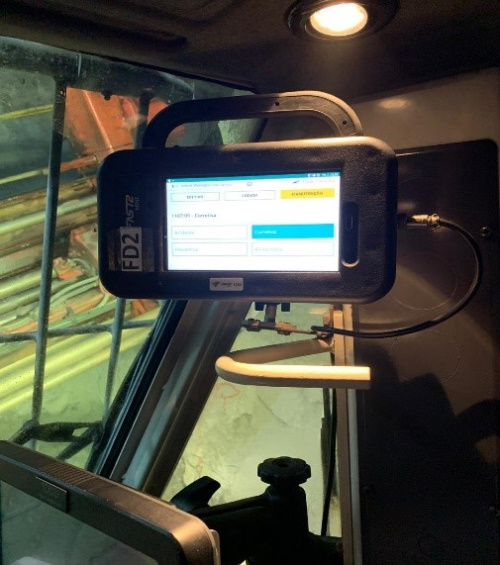
A primeira versão do Mining Control foi lançada em 2016 pela empresa Fast 2 Mine e implementada na Minerita, produtora de minério de ferro de Itatiaçu (MG). O sistema já contava com a gestão das frotas de carga, transporte e infraestrutura, além de um módulo de relatório para acompanhamento e tomada de decisão baseada nos KPIs dos equipamentos. Em 2019, foi lançado o Mining Control 2.0, com tecnologia de ponta e diversos novos módulos para gestão operacional da mina.
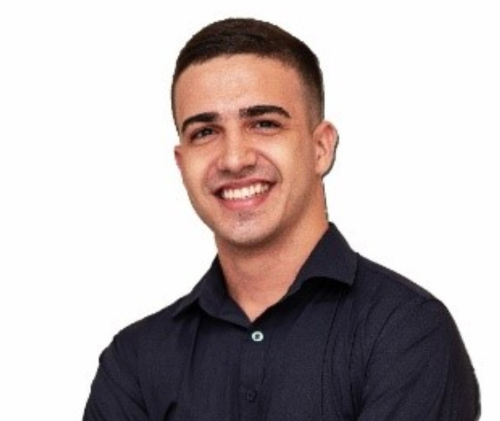
Com a implantação do sistema, diz o engenheiro júnior da MCSA, Felipe Mateus Leite Duarte, os principais resultados obtidos foram: a maior precisão das perdas e ciclos operacionais, gerando KPI’s mais confiáveis com os apontamentos realizados em tempo real e não após o término do evento; o controle de ciclo da frente de desenvolvimento, otimizando sua logística e a programação de fogos; a cronologia do tempo; a gestão das atividades improdutivas e produtivas dentro da manutenção dos equipamentos; e a agilidade na tomada de decisão, devido à rapidez de informações. Outros ganhos foram verificados na maior confiabilidade dos dados de diagnósticos de falhas e o perfil de perdas por frota, mapeando os sistemas, itens, modos e causa de falha.
Processo
A coleta dos dados no Mining Control ocorre em toda troca de turno, quando os tablets são sincronizados à rede wi-fi, enviando as informações registradas para um banco de dados SQL Server, onde são consolidadas via Business Intelligence (BI) para a elaboração automática de análises. Uma central autônoma guarda essas informações, garantindo a segurança dos dados. Na mina subterrânea da MCSA existem pontos estratégicos com wi-fi instalado, para a sincronização dos tablets.
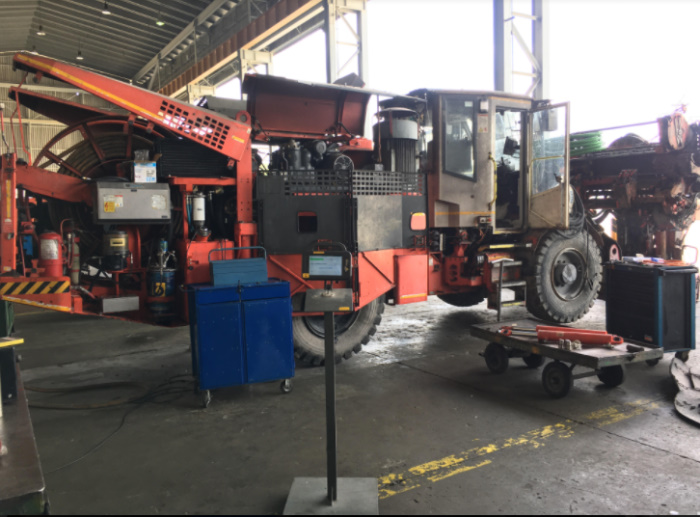
A frota monitorada pelo sistema inclui dois fandrills, dois cable bolting, três Cubex, cinco jumbos, seis rock boltings, seis betoneiras, quatro robôs projetados, dois raise borers, um shaft, uma planta de Paste Fill, cinco scalers, 22 caminhões e 11 pás-carregadeiras.
Em novembro de 2021, por exemplo, foram registradas 85 atuações de manutenções corretivas distribuídas nos sistemas existentes da frota Fandrill (Gráfico 01).
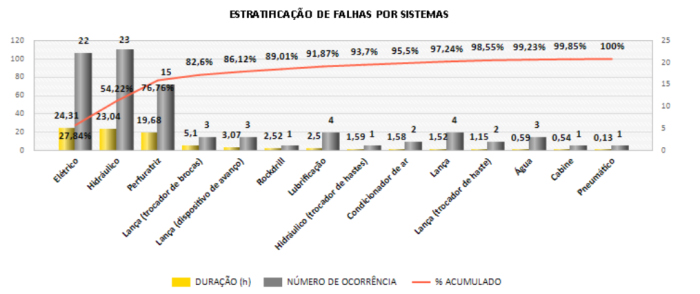
Após a elaboração e execução de um plano de ações para sanar essas falhas, apenas 16 atuações foram registradas nessa frota em janeiro de 2022, equivalendo a uma redução de 81,2% em relação à situação anterior (Gráfico 02).
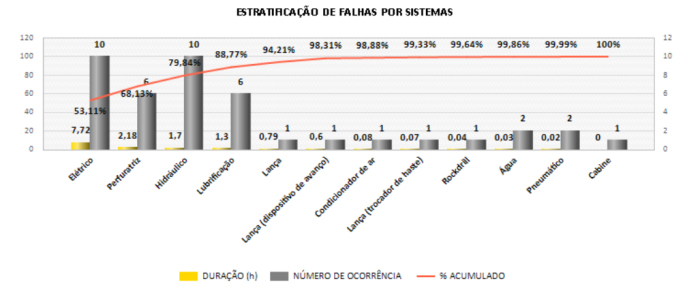
Para a implantação do Mining Control, explica a engenheira júnior da MCSA, Fernanda Pires Peña, foram realizadas reuniões entre mantenedores, supervisores e engenheiros da mineradora, visando o levantamento dos sistemas, itens e modos de falha de cada frota para cadastro no software. Também foram mapeadas as atividades produtivas e improdutivas que o sistema iria gerenciar. Posteriormente, foram feitos treinamentos com todos os mantenedores para a utilização do tablet durante sua atuação nas manutenções. Além disso, houve acompanhamento em campo pela equipe de engenharia para garantir a utilização correta do sistema.
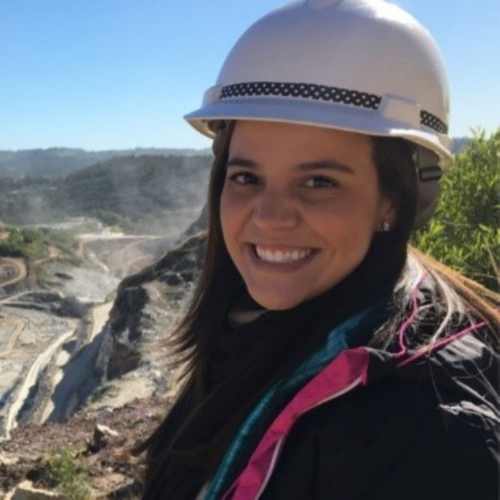
Antes de iniciar qualquer atividade, o operador deve preencher um checklist no tablet garantindo que o equipamento se encontra em boas condições para operar. Caso seja verificado algum desvio em qualquer item impeditivo do checklist, o equipamento passa automaticamente para o código de manutenção corretiva. O mesmo ocorre durante a operação da máquina: caso seja identificada alguma anomalia, o operador tem a opção de interromper a atividade e registrar que o equipamento está parado em manutenção corretiva no tablet, o que acionará a equipe de manutenção para correção da falha.
O sistema opera com dois tipos de manutenção: preventivas e corretivas. Na manutenção preventiva, utilizando o input por parte do mantenedor, é feito o gerenciamento das atividades produtivas e improdutivas da manutenção. Na manutenção corretiva, após a operação indicar que existe uma falha no equipamento, o mantenedor é informado. Ao chegar no equipamento, o log in no tablet registra os dados que alimentam o gerenciamento do sistema, como item, modo e causa de falha, além dos tempos produtivos e improdutivos. Essas informações seguem para o banco de dados utilizado pelo software para a composição de relatórios como o de perfil de perdas, que permite avaliar os pontos de melhorias no processo da manutenção, criando planos de ação direcionados a essas falhas e aprimorando os KPIs.